Corrosion Processes and Protection Systems

Nowadays, statistics indicate that at international level, industrialized countries lose about 6% of their Gross Domestic Product due to deterioration by corrosion phenomena in materials and coatings. Corrosion is a natural phenomenon that occurs in virtually every material in engineering, with the deterioration level depending upon the environment and the working conditions i.e. temperature, pressure, active species, flow rate, residual and applied stress level etc…to which they are exposed.
Processes materials in industries such as food, automotive, aeronautical, aerospace, chemistry and petrochemical, mining, cement and energy generation (fossil and nuclear) among others, can be seriously affected by phenomena of electrochemical or mechanical nature, or a combination of both (synergy).
To address this situation, the CIMAV´s Materials and Coating Deterioration Area develops technological projects, specialized technical services, consulting and training courses for companies interested in the improvement of the work capacity of materials in their production processes.
This group of specialists has a strong technical background, laboratory infrastructure and experience in the understanding and solution of material problems, from steel rebar in concrete structures to the assessment of corrosion performance of superalloys, and micro and high performance nanostructured coatings exposed to specific environments and conditions.
Laboratory and field work carried out by our team allow companies to prevent the incidence of materials failures in their processes, avoiding economical losses by production stoppages, worker’s security issues and/or damages to the environment.


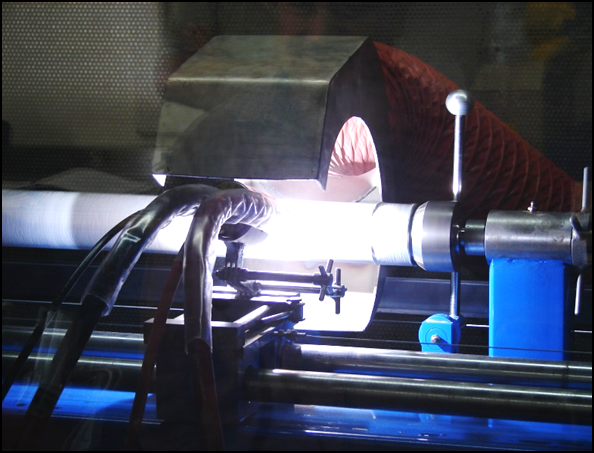
This research area has the Corrosion and Protection Laboratory (CPL), where specialized services ranging from quality control systems such as tests aimed at determining the efficiency of corrosion protection methods (corrosion inhibitors, coatings testing, electrochemical evaluation and material selection, among others) to the development of research projects related to high temperature corrosion and the determination of residual life of materials in energy and petrochemical plants, the effect of rare earths on the oxidation behavior of intermetallic compounds, as well as the analysis of high performance steels for the oil industry.
It is of great importance to notice that the Corrosion and Protection Laboratory has a number of first level accreditations, entering in this way to an exclusive list of specialized laboratories at national and international level. The EMA accreditation (Entidad Mexicana de Acreditación, A.C.) No. Q-102-021/19 and NADCAP accreditation (National Aerospace and Defense Contractors Accreditation Program) AC7101/6-Corrosión(Q) are a guarantee of the highest quality standard that a materials test laboratory can offer. Due to this fact, the Corrosion and Protection Laboratory can offer specialized technical services to the local, national and international industry dedicated to the production and testing of special materials.
The Materials Deterioration and Coatings Area has the potential to provide attention and support to industrial companies or higher education institutions.
This group has generated an important body of high impact publications in international journals in its area, having presence at national and international forums through oral presentations and conference publications, as well as a very important number of graduate students at masters and doctorate level.
Success Projects
The goal of the project was to carry out an estimation of the residual life of superheater tubes located in the high temperature and pressure zone in power in boilers for different private companies, using metallurgical analysis and obtaining corrosion velocities through ultrasonic techniques. The above, coupled with design data of the materials involved and the operating conditions, allowed us to do calculations using a specific software developed at CIMAV to assess the remaining life of the tubes located in critical zones in the boiler. This meant a great positive impact for companies regarding their preventive and predictive maintenance practices, optimizing the operation of their power generation units.
This project was done for the Air Force Office (AFO) of the United States. The aim was to analyze the behavior of superalloys and intermetallic materials (mainly Fe-Al, Ni-Al and Ti-Al systems) to determine the detrimental or beneficial factors influencing the adhesion and/or spallation of the protective oxide layers formed, looking to correlate the involved variables. In this project, a deeper knowledge in the understanding of the complexity of the process occurring during the high temperature oxidation phenomena for this kind of materials was attained, leading to possible improvements to the actual materials systems to extend its application range.
The problem of corrosion of stainless steel lines and welds in an oxide ethylene plant unit of a petrochemical complex was studied. Laboratory and field investigations indicated a strong deterioration problem due to stress corrosion cracking (SCC). The possible origin of residual stresses was determined in both base metal and welded joints, as well as the corrosive agents involved.
The analysis of materials and operation conditions, allowed us to propose recommendations from both an electrochemical point of view (to minimize the corrosive effect) and from a mechanical point of view (to reduce the stress levels in the components involved).
- Localised corrosion.
- Stress corrosión cracking.
- Atmospheric degradation of materials.
- High temperature corrosion (gas phase and molten salts).
- Erosion-corrosion processes.
- Corrosion and protection of rebar in concrete.
- Corrosion monitoring in real time.
- Failure analysis and residual life of materials.
- Synthesis and evaluation of corrosion inhibitors.
- Nondestructive testing.
- Inspection and evaluation of metallic, organic and inorganic coatings.
- Development, implementation and evaluation of coatings applied by plasma thermal spray systems for biomedical and industrial applications, etc.
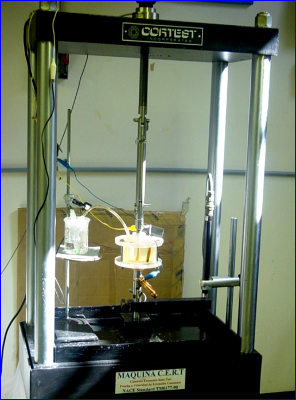